Case Studies
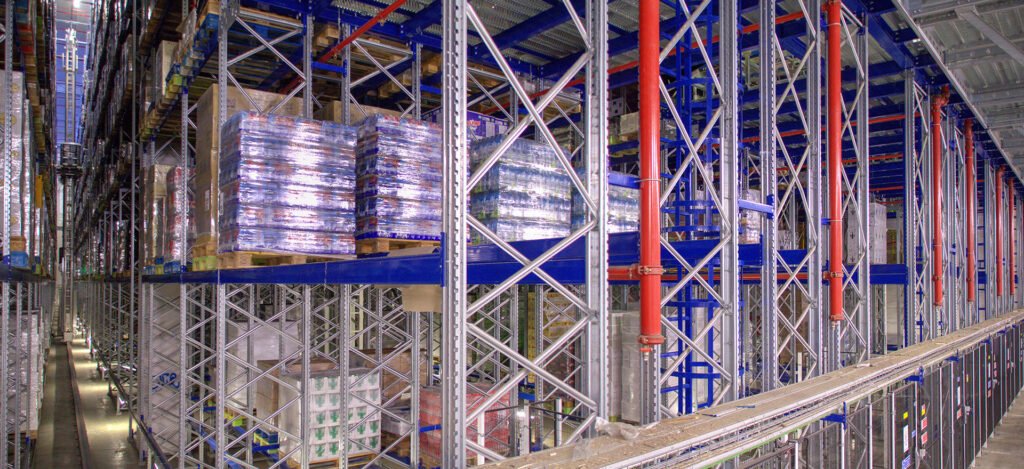
Objective: Efficiently Retrieve A Variety Of Heavy Parts With Precision And Speed.
Introduction: In the dynamic operational landscape of the Indian Navy, the imperative is precision and swiftness. The primary objective is to institute a system that guarantees the accurate and rapid retrieval of a diverse array of heavy components within tight timelines. This pursuit aims not only to meet the critical demands of naval operations but also to elevate the overall operational efficiency. In navigating the challenges of a maritime environment, the focus is on implementing a solution that aligns seamlessly with the need for precision and speed in retrieving vital heavy parts.
Problem Statement:
To meet the challenge head-on, a tailored Automated Storage and Retrieval System (ASRS) was seamlessly integrated with the Indian Navy’s central system. This innovative solution combined static racks and a stacker crane mechanism, eliminating manual labor entirely, especially in dealing with heavy materials. Integration with a conveyor belt further streamlined material movement, while barcodes ensured precise, automated material tracking. The system not only enhanced operational efficiency but also significantly increased safety for users and storekeepers. With a reduction of up to 80% in storing and retrieving times, the ASRS system proved to be a game-changer. The integration with the central system facilitated seamless inventory management, and system-driven alerts for sample expiry provided enhanced control over storage processes.
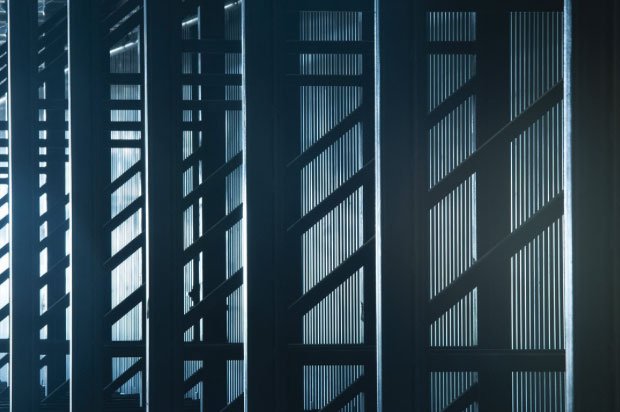
Solution:
To address the critical challenge faced by the Indian Navy, a robust solution was implemented, integrating a customized Automated Storage and Retrieval System (ASRS) with the central system. This cutting-edge solution revolutionized the storage and retrieval processes, offering a range of features aimed at enhancing efficiency, accuracy, and overall operational effectiveness.
Combination of Static Racks and Stacker Crane Mechanism:
The ASRS solution strategically combined static racks with a stacker crane mechanism, optimizing storage space and facilitating the efficient retrieval of heavy parts.
Elimination of Manual Labor:
The system resulted in a complete stop in manual labor related to storing or retrieving materials, especially heavy components, ensuring not only efficiency but also safety in material handling.
Integration with Conveyor Belt:
A key highlight was the integration of the ASRS with a conveyor belt, streamlining the process of sending or removing materials from bins. This integration significantly reduced material transfer times.
Barcode Integration for Accuracy:
Barcodes were seamlessly integrated into the system, ensuring the most accurate material inward and outward entries. This automation eliminated the risks associated with manual data entry and enhanced overall accuracy.
Increased Safety Measures:
The system implementation prioritized safety, providing increased safety measures for both users and storekeepers, minimizing the risks associated with manual material handling.
Significant Time Reduction:
With the customized ASRS, a remarkable time reduction of up to 80% in storing or retrieving materials. This efficiency gain directly contributed to improved overall productivity.
Seamless Integration with Central System:
The ASRS was seamlessly integrated with the central system of the Indian Navy, fostering smooth communication and data exchange. This integration facilitated real-time updates and enhanced overall inventory management.
System-Driven Alerts for Sample Expiry:
An intelligent feature included system-driven alerts for the expiry of samples, providing proactive control over the storage and usage processes. This preventive measure ensured better management of material quality and compliance.
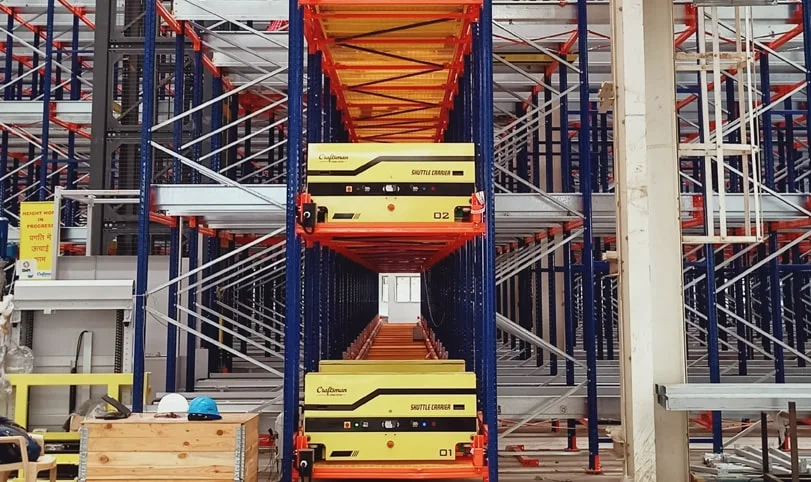
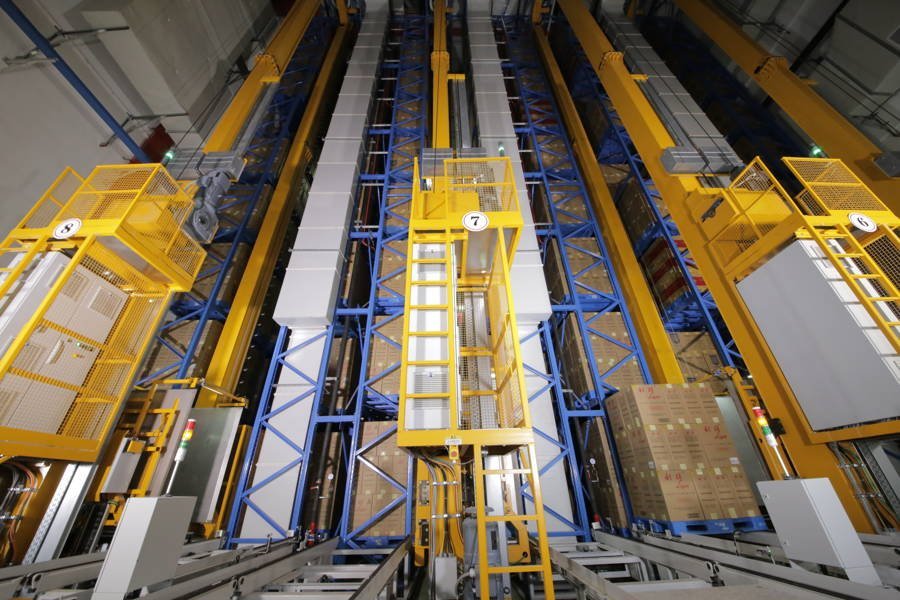
Benefits:
Unprecedented Efficiency Gains:
The implementation of the customized ASRS resulted in unparalleled efficiency gains, significantly reducing the time required for material retrieval. This directly translated to faster production cycles, enhancing overall operational throughput.
Optimized Space Utilization:
The vertical design of the ASRS system maximized space utilization, unlocking valuable floor area that could be repurposed for other critical operational needs. This space-saving feature contributed to a more organized and resource-efficient environment.
Labor Cost Reduction and Automation:
The automation of the retrieval process led to a substantial reduction in labor costs. By eliminating manual labor associated with material handling, the organization achieved long-term cost savings while simultaneously enhancing workplace safety.
Heightened Accuracy and Product Quality:
The automated retrieval process integrated with barcodes ensured heightened accuracy in material tracking. This not only minimized the risk of errors but also mitigated the potential for material damage, resulting in a significant enhancement in overall product quality.
Streamlined Operations Across the Workflow:
The integration of the ASRS seamlessly streamlined operations across the entire workflow, from material retrieval to production. This comprehensive integration led to smoother workflows, reducing bottlenecks and improving the overall operational rhythm.
Scalability for Future Growth:
Leveraging the modular nature of the ASRS system, the advantage of scalability. As the organization’s needs evolve over time, the system can be easily expanded to accommodate increased demands, providing a flexible and future-ready solution.