Case Studies
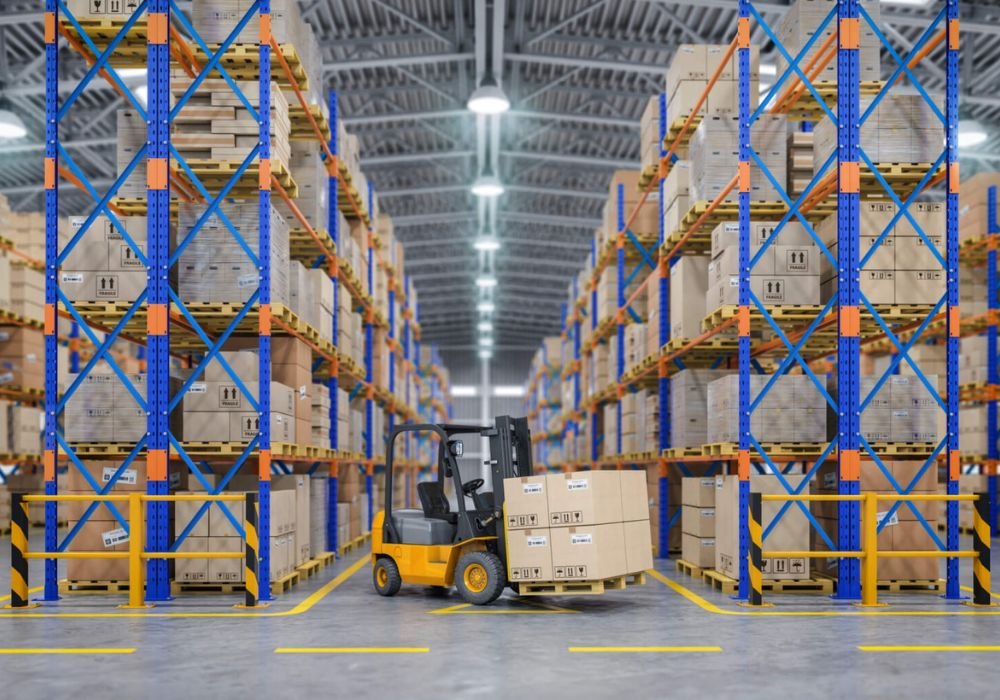
Project Details
Client Profile:
An Engineering Solutions and Services
Engineering, Transformer Manufacturing
Solution :
LeanStore System
Objective: Efficient Storage And Retrieval Of Various Transformer Raw Materials
Introduction: Our client is an Engineering Solutions and Services organization and leading player in the engineering industry, specializing in the design, manufacturing, and servicing of various types of transformers, including power, earthing, furnace, cast resin, and vacuum-impregnated transformers, Gas Meters, Busbars, Isolators etc. As the demand for their products grew, the organization faced challenges in managing and retrieving the diverse raw materials required for transformer manufacturing. The need for a streamlined storage and retrieval process became evident to optimize operational efficiency and meet growing customer expectations.
Challenges:
Diverse Raw Materials: Transformer manufacturing involves a wide range of raw materials, each with varying sizes and weights. Efficiently organizing and accessing these materials was becoming increasingly complex.
Space Utilization: The available floor space for storage was limited. Traditional storage methods led to congestion, making it difficult to locate and access specific materials in a timely manner.
Time Consumption: Manual retrieval of heavy materials using traditional methods like forklifts and manual labor was time-consuming and risk-prone, affecting overall production timelines.
Operational Costs: Labor-intensive retrieval methods and inefficient space utilization were leading to increased labor costs and reduced productivity.
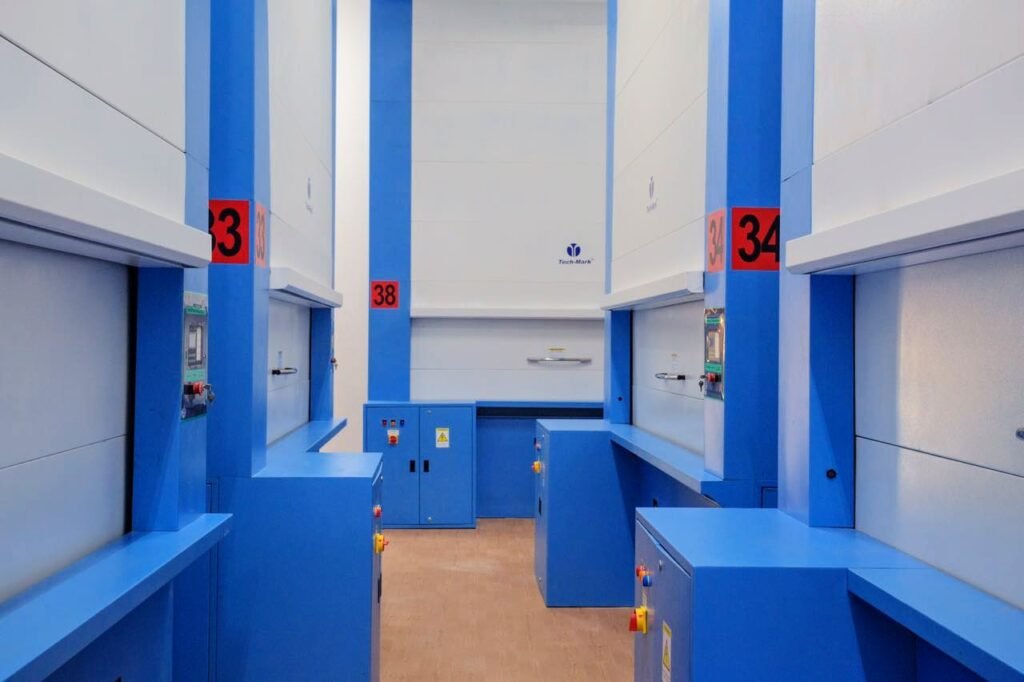
Solution:
LeanStoreTM To address these challenges, the client decided to integrate a LeanStore System into their manufacturing facility. This cutting-edge solution offered a streamlined approach to storing and retrieving raw materials for transformer manufacturing. The system’s features included:
Diverse Tray Capacities: The system was designed to accommodate various tray sizes, allowing the storage of different raw materials in a single system.
Tray Carrying Capacity: Each tray had a maximum carrying capacity of 1.5 MT, ensuring compatibility with the heavy raw materials used in transformer manufacturing.
Tray Extractor System: The system featured a specially designed Tray Extractor mechanism that accurately retrieved the required tray from the storage system, minimizing human intervention and reducing the risk of errors.
Material Retrieval Mechanisms: Raw material retrieval could be performed using either an EOT (Electric Overhead Travel) crane or a system-mounted electric hoist, providing flexibility based on material weight and dimensions.
Optimized Space Utilization: The vertical design of the storage system allowed for efficient utilization of floor space, reducing congestion and enhancing overall storage capacity.
Inventory Management: The system was integrated with an inventory management software that provided real-time visibility of available materials, simplifying material tracking and reordering.
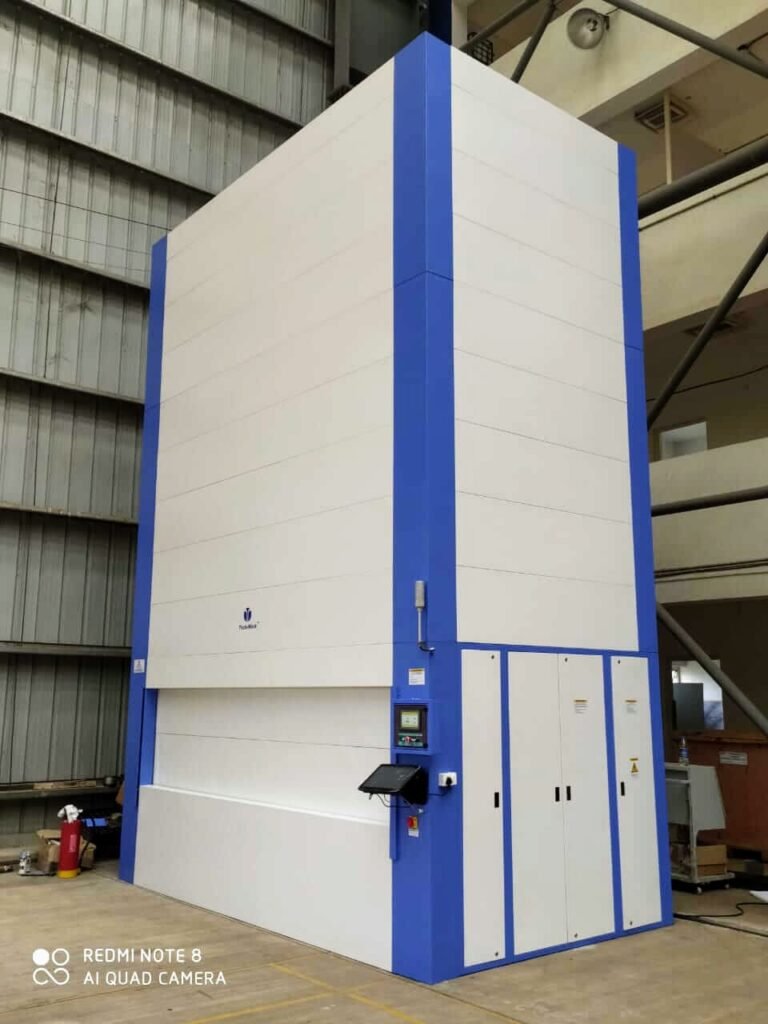
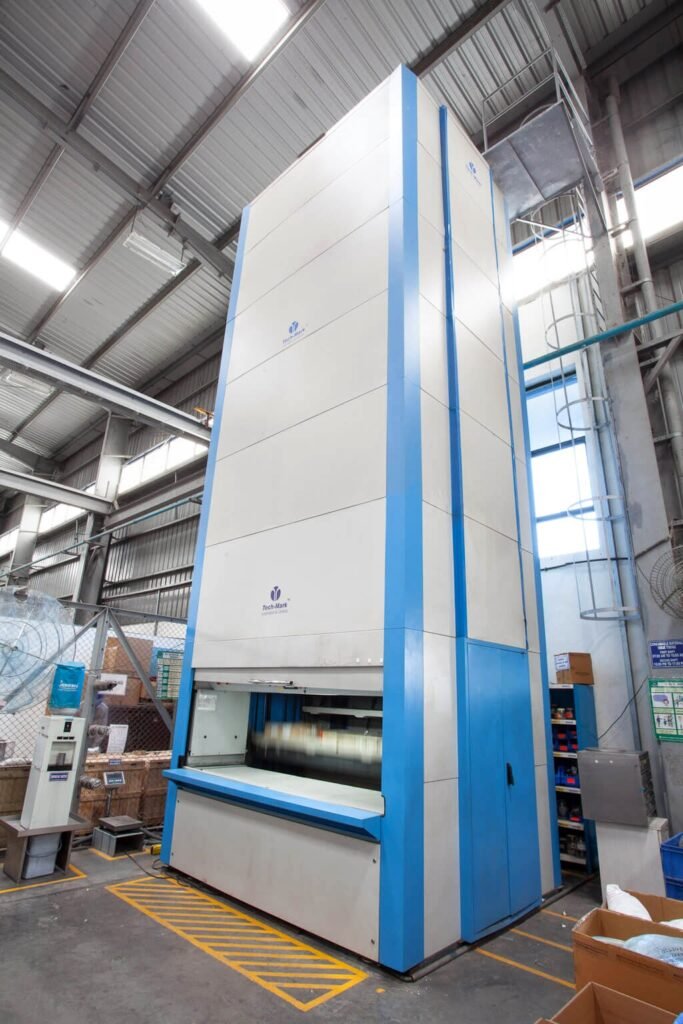
Benefits:
Enhanced Efficiency: The LeanStore System significantly reduced the time required for material retrieval, contributing to faster production cycles.
Space Savings: The vertical design optimized space utilization, freeing up valuable floor area for other operational needs.
Reduced Labor Costs: Automation of the retrieval process reduced the need for manual labor, leading to cost savings in the long run.
Improved Accuracy: The automated retrieval process minimized the risk of errors and material damage, enhancing overall product quality.
Streamlined Operations: The integration of the system streamlined operations, from material retrieval to production, resulting in smoother workflows.
Scalability: The modular nature of the system allowed for easy expansion as the organization’s needs evolved.